Navigating the World of Fasteners and Machining: Approaches for Precision and Rate
In the intricate realm of fasteners and machining, the quest for precision and speed is a continuous challenge that demands meticulous attention to detail and strategic planning. From understanding the varied range of fastener kinds to picking optimum products that can hold up against rigorous demands, each step in the process plays a critical role in achieving the wanted end result.
Understanding Bolt Kind
When picking fasteners for a project, comprehending the various types readily available is important for ensuring ideal efficiency and integrity. Screws are used with nuts to hold materials with each other, while screws are versatile fasteners that can be made use of with or without a nut, depending on the application. Washers are necessary for dispersing the load of the bolt and protecting against damage to the material being attached.
Picking the Right Materials
Comprehending the value of picking the best products is extremely important in ensuring the ideal performance and dependability of the picked bolt kinds discussed formerly. When it involves bolts and machining applications, the material selection plays a vital function in figuring out the total toughness, sturdiness, deterioration resistance, and compatibility with the desired setting. Various products supply differing properties that can considerably affect the efficiency of the bolts.
Usual products utilized for fasteners include steel, stainless steel, brass, light weight aluminum, and titanium, each having its one-of-a-kind toughness and weak points. Steel is renowned for its high toughness and longevity, making it ideal for a variety of applications. Stainless steel supplies superb deterioration resistance, suitable for atmospheres prone to moisture and chemicals. Light weight aluminum is light-weight and corrosion-resistant, making it suitable for applications where weight reduction is essential. Brass is commonly chosen for its aesthetic charm and exceptional conductivity. Titanium is recognized for its extraordinary strength-to-weight proportion, making it optimal for high-performance applications. Choosing the appropriate material includes considering variables such as toughness demands, ecological problems, and budget restraints to make sure the desired efficiency and longevity of the bolts.
Precision Machining Techniques
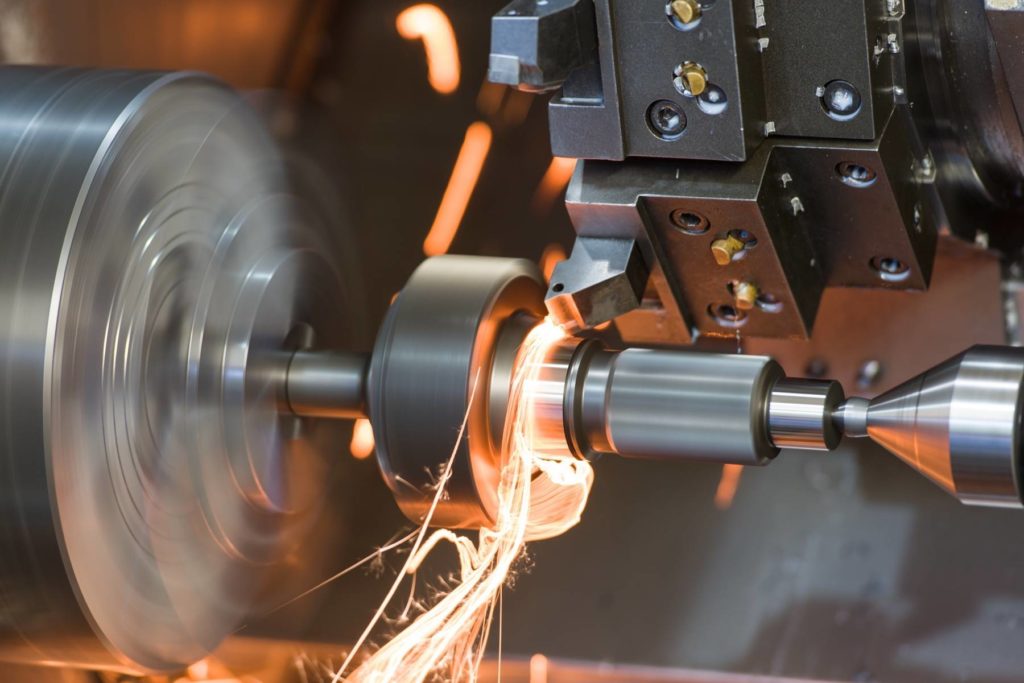
In enhancement to CNC machining, other precision strategies like grinding, turning, milling, and boring play vital functions in bolt production. Grinding assists accomplish fine surface coatings and tight dimensional tolerances, while transforming is frequently utilized to develop cylindrical elements with specific diameters. Milling and boring procedures are essential for shaping and producing openings in bolts, ensuring they satisfy specific specifications and function properly.
Enhancing Rate and Performance
To optimize fastener manufacturing procedures, it is vital to streamline operations and execute effective approaches that complement precision machining techniques. One crucial method for enhancing speed and effectiveness is the application of lean production concepts. By reducing waste and concentrating on continuous improvement, lean practices help maximize and remove traffic jams operations. In addition, buying automation modern technologies can significantly improve production rate. Automated systems can handle repetitive jobs with accuracy and rate, enabling workers to focus on more complicated and value-added activities. Adopting Just-In-Time (JIT) inventory management can additionally boost effectiveness by making sure that the ideal materials are offered at the appropriate time, reducing excess stock and decreasing lead times. Additionally, cultivating a society of see this website cooperation and communication among staff member can enhance total performance by promoting you can look here transparency, problem-solving, and innovation. By integrating these techniques, manufacturers can attain a balance in between speed and precision, inevitably improving their affordable edge in the bolt sector.
Top Quality Control Measures
Applying rigorous top quality control procedures is crucial in making sure the dependability and consistency of bolt items in the manufacturing procedure. Fasteners and Machining. Quality control procedures include various phases, starting from the selection of raw products to the final inspection of the completed fasteners. This entails examining elements such as material toughness, composition, and toughness to assure that the fasteners fulfill market criteria.
Regular calibration of devices and equipment is imperative to preserve uniformity in production and make sure that bolts meet the necessary resistances. Implementing stringent methods for identifying and addressing non-conformities or flaws is vital in avoiding substandard items from getting in the market. By establishing a thorough quality control framework, suppliers can copyright the track record of their brand name and supply fasteners that meet the greatest requirements of efficiency and resilience.
Conclusion
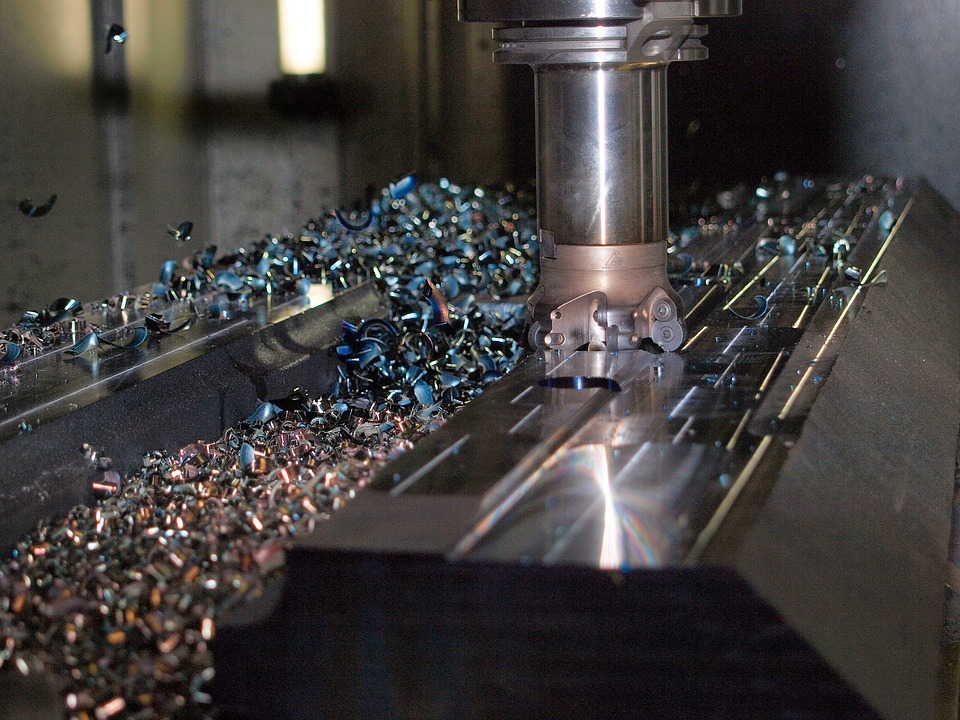
In the complex realm of fasteners and machining, the mission for precision and speed is a perpetual difficulty that requires careful interest to information and calculated preparation. When it comes to bolts and machining applications, the material choice plays a vital duty in determining the general toughness, longevity, deterioration resistance, and compatibility with the desired setting. Accuracy machining includes different advanced methods that ensure the limited tolerances and specifications needed for bolts.In enhancement to CNC machining, other accuracy strategies like grinding, turning, milling, and boring play important duties in bolt manufacturing.To optimize bolt production processes, it you can try here is important to improve operations and execute efficient strategies that enhance precision machining techniques.